Introductory
Choosing and SelectingThe Right Clay Body
When making any decision or researching selecting the right clay body for your application, you need to consider the end product, cost and skill level. When choosing a clay, you also need to know what type of kiln you have access to and it's temperature limits. Each clay has a specific temperature range specifications. You may find that you want to use more than one clay body if you use a variety of construction methods such as potter's wheel or hand building. We learned that before selecting the clay that will be best to use, there are many variables to consider, and in wanting to share the knowledge we gained from our experiences, we put together the tutorial below.
What is clay
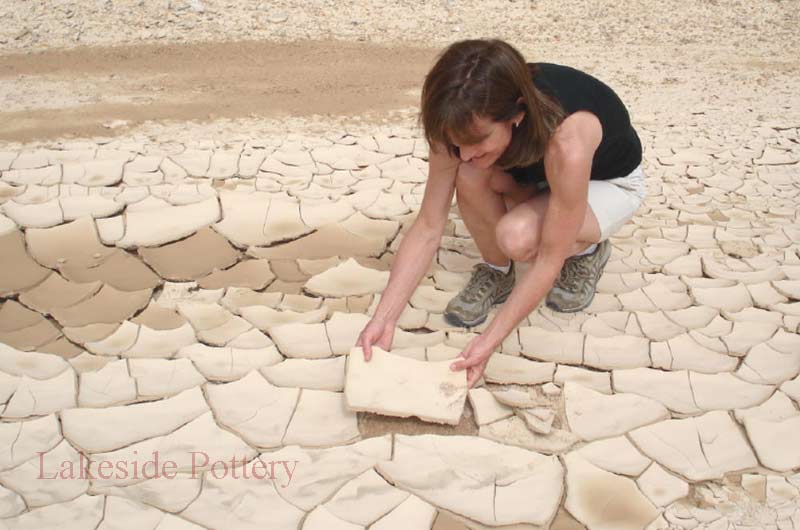
Clay is made up of the finest particles of rock eroded by wind and rain which are carried off by running water. These particles gather at the bottom of rivers or streams where they stick together and are compacted. Clay can be found almost everywhere and it is cheap. It has several transitional states; it is squishy and elastic when it is wet, and you can make any shape you like. When it dries slightly it becomes the consistency of chocolate or cheddar cheese and can be carved or scraped. It dries further, pretty quickly depending on its thickness and the humidity, as the water evaporates out into a brittle state. At this point, it can be made soft again by getting it wet. So whatever shape the clay is made, it will not be permanent until it is heated to high temperatures.
Important Terms:
Wet clay: Mixed clay ready to be formed, at the clay's most elastic state
Leather-hard: A stage in the drying process when a clay object can be carefully handled without danger of the shape being deformed, but the clay is still pliable enough so alterations can be made if desired
Greenware: A stage in the production of pottery where a vessel is going through the drying process necessary before it can be safely fired.
Bone dry: Completely air dry clay, at its most brittle state, like a biscuit
Bisque: An intermediate step in firing (also called: first firing). The vessel is porous after being fired giving it the ability to the absorb water of the glaze solution causing the glaze materials to adhere to the piece while it maintains its shape
Grog: A sand-like substance that is added to a claybody to add workability, strength and helps to reduce shrinkage of the clay.
What is Ceramic
Ceramic is heat-resistant, nonmetallic, insulators (does not conduct electricity), corrosion-resistant, hard, but brittle (like glass), inorganic solids made out of clay that has been fired to high temperature. Once the clay is fired to high temperature, it's chemical composition permanently changes and becomes Ceramic which will never dissolve in water again. Anything that is made from fired clay is ceramic including table ware, pots, oven ware, brick, tile, roof tile, bathtroom fixtures (e.g., sink), etc. The following terms all fall under ceramic: Pottery, china, porcelain, stoneware, earthenware
Shrinkage and Weight Loss
Clay shrinks both in drying and in firing. Different clay bodies shrink at different rates which can be as little as 4%, or as much as 15% for some clay bodies. Even one percentage point can make a difference in the final product depending on your need for precision. Your choice of clay and ware design, therefore, needs to account for the shrinking for the temperature to which you fire. For example, the clay we use at Lakeside Pottery is Standard's Baldwin 192 and it is specified to shrink 11% for cone 6 firing temperature. Our testing showed that about 5% shrink during the drying process, 1/2% during bisque firing (cone 06) and 5.5% during glaze firing (cone 6). The total of 11% is shown in the lantern picture below (before and after).
We also found through years of firing, that even with the same clay body, shrinkage can vary 1-2% from batch to batch. Where accuracy is important, we run a batch test before proceeding with a project or tell our commission customers to expect +/- 3% variance. More about drying and firing.
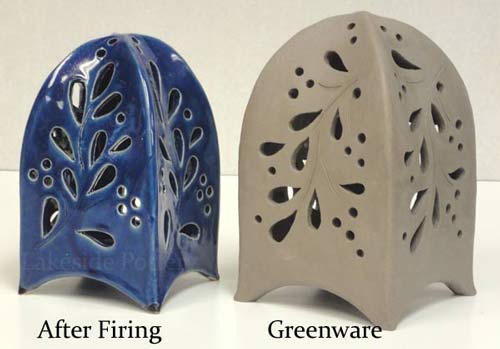
11% shrinkage clay spec will look like the above comparing
wet clay to finished product (stoneware / cone 6)
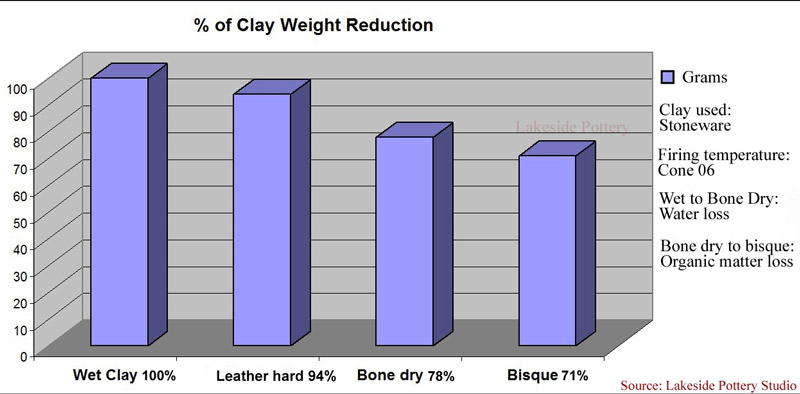
Average clay contains about 20% water and 9% organic matter, thus, finished pots (bisque or glazed) weigh almost 30% less than the initial clay weight.
Firing Temperatures
There are three basic temperature ranges. Although there is some slight variation between individual potters, these ranges are generally considered to be
- Low-Fire: Cone 06 to Cone 3 (1850 °F - 2135°F)
- Mid-Range: Cone 4 to Cone 7 (2160 °F - 2290°F)
- High-Fire: Cone 8 to Cone 10 (2315 °F - 2380°F)
What Happens to the clay during firing?
During the complete cycle of clay firing in a kiln, the clay goes from totally fragile substance (clay) to stone like substance (ceramic) impervious to water and time. After the clay has completely air dried, "Bone dry", and placed in the kiln, the firing consists of several stages outlined below.
1) Burn Off of Carbon and Sulfur
Clay bodies all contain carbon, organic materials, and sulfur which will burn off between 570°F and 1470°F (or 300°C and 800°C).
2) Chemically Combined Water Driven Off
After the clay is air dried, it still contains about 15% of water which are chemically bonded. Chemically, clay is defined as being a molecule of alumina and two molecules of silica bonded with two molecules of water. The chemically combined water bond loosens when heated during the same time as the Carbon and Sulfur burn off. The chemically bonded water escapes from the clay body between 660° F and 1470°F (350° C and 800° C). The pot will become substantially lighter with no physical shrinkage. It is critical that during this stage, the temperature rise is slow to prevent rapid steam escape which can result in explosion.
3) Quartz Inversion
Quartz, also called silica oxide, has a crystalline structure that changes at a temperature of 1060°F (573°C). This change (Quarts Inversion) in crystalline structure will cause the pottery to increase in size by 2% while heating and loose this 2% when cooled. The ware is fragile during this change and kiln temperature must be raised.
4) Sintering / Bisquing
Starting at about 1650°F (900°C) the clay particles begin to fuse. This process is called sintering that when completed, the clay has become ceramic. Once temperature reached between 1800°F (cone 06) to 1950°F (cone 04) it is bisquied. At this stage, the ceramic porous, somewhat fragile, not yet vertified and is called Earthenware or Bisque. The Bisque allows wet, raw glazes to adhere to the pottery before Glaze firing.
5) Vitrification and Maturity
Vitrification is the progressive fusion of a clay that makes the finished product harder and more durable. As vitrification proceeds with temperature increase, the proportion of glassy bond increases and the porosity of the fired ceramic becomes lower.
It is also during this stage that mullite or aluminum silicate crystals are formed that act as a binder strengthening the clay body even further.
Glazing alone does not make pottery impermeable to water in most cases. However, Porcelain which is among the most vertified ceramic is impermeable even without glaze. Stoneware is semi-vitrified and would not be impermeable without glaze
6) Cooling
The crystalline form of silica, as it cools past 420°F (220°C) must be cooled slowly as it moves through this critical temperature to avoid cracks.
See more about clay drying and firing
Criteria of Choosing Clay Body
1) The Making Process: Hand Building, Pottery Wheel, Sculpting or Casting
2) Size and form of your work
3) Surface Texture
4) Firing temperature and Type
5) End product usage
6) Clay color glaze effect
Hand Building Clay Body
The primary requirement of a hand building clay body is strength and plasticity.
Strength
Strength is the ability of the formed clay to hold firmer as the shapes are constructed, handled and attached without sagging, stretching or cracking. Hand built forms need a high degree of strength in the greenware stage. Strength becomes even more important as the hand built objects are larger or more flat. Higher ratio of grog (5% to 30%) is typical for hand building choices. The grog can either be fine or coarse, depending on the surface qualities the potter wants. Such high additions of grog also results in quicker clay air drying time and with a reduction in the possibility of cracking during the drying process.
Plasticity
A hand building project will also need plasticity to be workable. The more extreme the shapes being built (e.g., sharp angles or coiling), the more plasticity the clay will need.
Throwing Clay Body
There are three characteristics necessary for a clay body for throwing: a) high degree of plasticity, low rate of water absorption and c) strong enough to hold their shape while being worked (squeezed, turned, gravity force, pulled and pushed).
Plasticity
Plasticity is the most important characteristic needed for throwing to make workable and movable on the pottery wheel. Ball clay or porcelain are highly plastic and are often used for throwing. However, the more plastic a clay is, the more it will shrink and therefore has greater potential to warp while drying.
Strength
Throwing clay must have enough strength to stand upright when thrown into taller forms. To achieve the strength, the throwing clay bodies contain some particles such as sand or grog or both. When grog is used in a throwing body, it needs to be finer to provide the strength without being too coarse to hurt the potter's hands. In general, a throwing clay body should contain no more than 7 to 9% of particled additives.
Water Absorption
The longer a clay is worked on the potter's wheel, the softer it becomes as the water mixes with the clay increasing the chance of collapse and limiting the vessels size / height. Water absorption rate therefore is an important factor. Plastic clays absorb less water than clay with coarse materials and are on the stiff side. This also means that the clay is harder and more tiring to work with a possibility hurting muscles and joints. Therefore, a good throwing clay must be balanced between plasticity, strength, and water absorption.
Classes of Clay Body
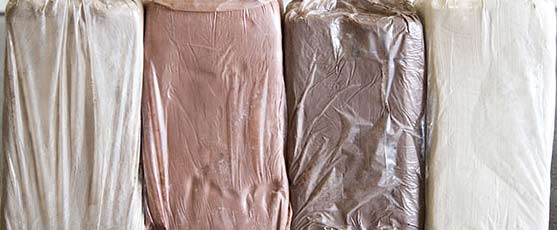
There are so many choices of clays and it can be hard to choose the right one for you. How do you choose which clay is right for you and your needs as a potter? What do you need to know? How do you find out?
The three most commonly used clay bodies are earthenware, mid-fire stoneware, high-fire stoneware and porcelain. All three are available commercially in moist and ready to use 25 lbs packages. Clay bodies can also be produced by mixing dry clays and additives with water to create your own desired clay body for specific applications and cost savings.
Earthenware Clays
Earthenware clays are the oldest known to ancient potters and it is the most common naturally found. These clays are highly plastic easy to work with. Earthenware clays contain iron and other mineral impurities which cause the clay to reach its optimum hardness at lower temperatures between 1745°F and 2012°F (950°C and 1100°C) resulting in softer, unvitrified (not turned into glass) yielding porous ceramic enabling rich clay colors post firing, low shrink factor and can be stained easily. Unglazed earthenware, such as terra cotta, is porous and not watertight. Earthenware is more forgiving than clay with finer particles. It is common in nature and it used primarily for bricks, tiles and planting products. Earthenware will not work well for vessels that holds liquids (e.g., vases, mugs, pitchers) unless glazed. Glazed earthenware products tend to be more fragile than glazed stoneware products. Typical colors for most earthenware clays are red, orange, yellow, and light gray. Colors for fired earthenware includes brown, red, orange, buff, medium gray, and white. Fired colors are mostly determined by the content of mineral impurities and the type of firing. Because the glaze firing is at a lower temperature, glaze colors tend to be more vivid than stoneware glazes that are fired at higher temperatures.
Stoneware Clays
Stoneware clays are plastic and are often gray when moist. Their fired colors range through light gray and buff, to medium gray and brown. Fired colors are greatly affected by the type of firing.
Stoneware clays have an absorption factor of about 2 to 5 percent, and are usually fired to temperatures ranging from 2100 degrees to 2372 degrees F (cone 3-cone 11). Stoneware clays are named "Stoneware" because the fired pots exhibit stone-like characteristics (hard, dense surface with variegated color). Stoneware bonds well with its glazes, and should be leak-proof after firing to maturity. It is tough and forgiving during throwing and firing stages. Stoneware is very common clay for production potters.
Fired stoneware colors ranging from buff or light gray to brown or dark gray. Because of its hard, tight qualities, this clay is an excellent choice for functional applications such as dinnerware. The higher the maturing temperature of stoneware clay, the more durable and more water proof is the ware.
Porcelain / Kaolin / Ball Clays
Porcelain and kaolin clay are used for high-quality ware including laboratory equipment. Porcelain and kaolin clays are virtually identical and are considered the best clays available for making pottery. They are also the most expensive. They are a largely silicate clay and are resistant to high temperatures. If you want to make high-quality ware, then this type of clay is best for you. The pottery will likely be white or pale in color unless you buy clay that has been mixed with iron oxide to make it redder.
Porcelain, characterized by an absorption rate of 0 to 1 percent, is the product of many hundreds of years of development by early Chinese potters. Its main ingredient is Kaolin, also known as china clay. By itself, Kaolin has a melting point of around 3275 degrees F, and is difficult to form because of low plasticity. To achieve the dense, hard, white, translucent clay body known as Porcelain, Kaolin is mixed with other clays to achieve a high degree of workability and to lower the firing temperature. Typically, Porcelain is fired at temperatures above 2300 degrees F (cone 9), yet can be formulated for firing at temperatures as low as 1900 degrees F (cone 04*) by adding unusual ingredients.
Because it's composed of such tiny particles, porcelain offers optimum qualities of smoothness, and can be manipulated even when extremely thin to achieve translucent, delicate forms. However, it is difficult to work with during the throwing stage because of its low plasticity. It cracks and deforms easily during the drying and firing stages, because its optimum density isn't achieved until nearly the melting point of the clay.
Ball clays are highly plastic and contain few mineral impurities. They fire to their mature hardness at about 2340°F (1300°C). When moist they are dark gray and when fired they are either light gray or light buff. Ball clays do have a serious drawback. They cannot be used by themselves due to their excessive shrinkage during drying and firing. They are extremely useful, however, when added to other clays to increase workability and plasticity.
Clay Colors
Clays come in white, off white and dark colors such as Terra Cotta. The areas effecting your decision are the effect of glazing on the finished ware and studio maintenance.
Effect of Glazing
We have several test tiles using the same glaze on different clays and some of the glazes, (in particular translucent glazes), the end results are very different. Make sure you test the possible clays with your glazes first before committing to a large clay or glaze quantity
Studio Maintenance
Dark clay colors, in particular Terra Cotta, make a big mess. Much harder to clean (floor, tools, hands) and can stain your clothing. If choosing more than one clay remember that you'll have to have recycling bin for each type and wedging board should not share dark and light clay to avoid color contamination.
Mixing Clays Applications
If two clay types are used in the same vessel (not recommended), the shrink rate will mostly be different and separation could occur during the drying and/or the firing process. In our case, we run into an issue where we wanted to use slip (slurry) as decorative surface texture but given the grog level in the type of stoneware we use, the end effect was rough and not appealing. We considered making or purchasing slip made of a different grog-less clay but separation and color differences would have been an issue. Our solution was to make the slip (see link on how to make slip) and sieve it twice with 100 mesh screen. This solution worked perfectly for almost 15 years now.
|