After using and repairing our Skutt kilns for many years, we have listed below the most common issues of electric kiln failures and solutions to guide you through. Always follow the kiln's manufacturer procedures and safety instructions.
1) No LED or Power indicator shown in the controller
|
a. Shut off switch is turned off
|
|
|
|
|
|
b. Plug is not connected or corroded
|
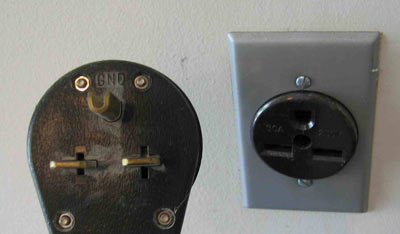 |
|
|
i. Connect plug
ii. Unplugged and inspect for corrosion |
|
|
|
c. Loose power wire
|
|
|
|
i. Service kiln’s wires and possibly replace connectors
|
|
|
|
d. Computer box fuse is blown
|
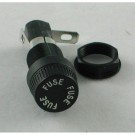 |
|
|
i. Replace fuse
ii. If fuse is blown after replacing it, controller box is defective
|
|
|
|
e. Defective controller board
|
|
|
|
i. Replace controller board
|
|
|
2) Kiln turned off while running with an error message
|
b. Electric power failure. Even a short power loss will turn off the kiln.
|
|
|
|
i. Restart kiln. Note that if kiln turned off at temperature above 1000 degree F and it is glaze firing, glazes might fail (crackle, crawl, different colors, broken ware).
|
|
|
|
d. The temperature is rising faster than the maximum allowed by the computer’s program
|
|
|
|
|
|
e. Room temperature is too hot
|
|
|
|
i. Add room venting / cooling
ii. Place in a larger room
|
|
|
3) The kiln will display “Complete” but will not cool off
|
a. A relay is stuck
|
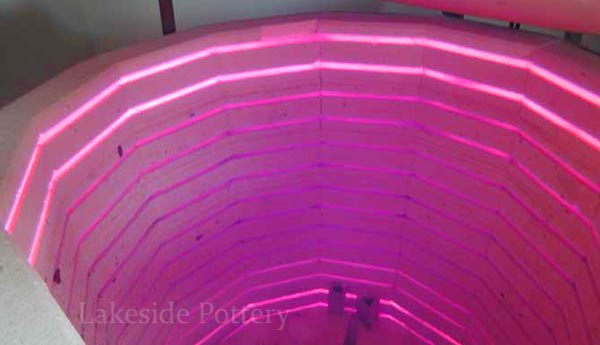 |
|
|
i. Check and see which element is still glowing and replace the corresponding relay
ii. Relays get stuck more often if kiln is running in a cold room. Warm the room to over 60 degrees F before operating the kiln.
|
|
|
4) The thermocouple is flaking
|
a. Clean with a brush and inspect for over thinning
|
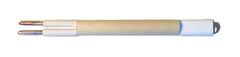 |
|
|
i. Replace thermocouple if too thin
|
|
|
5) My normal firing duration increases
|
a. Check thermocouple thinness
|
|
|
|
i. If too thin, replace
ii. K style thermocouples need to be replaced about every 30-50 firings.
|
|
|
|
b. Elements are getting older (corroded with thinner cross section and therefore increased resistance which reduces the emitted temperature.
|
|
|
|
i. Replace elements. If waiting too long, computer will eventually shut off kiln during firing or an element will break.
|
|
|
|
c. One of the kiln's phases (if three phase) is off.
|
|
|
|
i. Verify with a voltmeter that all three phases are present
ii. Check of all three phases circuit breakers are on.
|
|
|
6) What effect will longer firing time have on my ceramic ware
|
a. With bisque firing no effect
b. With glaze firing, the firing time extension due to worn elements or a broken element will be toward the end of the firing. Therefore, the glazes will be exposed to high temperature longer than typical and be in a liquid form for longer. Thus, glaze performance will change and might end up on the kiln shelves.
|
|
7) How often should I change my kiln’s elements and relays to avoid failure during firing
|
a. If firing to Cone 5-6, about every 80 firing
b. Record each firing duration. When start seeing increase firing duration by over 30 minutes, time to change elements and relays
c. APM industrial elements last up 4 times longer but cost about 4 times more.
|
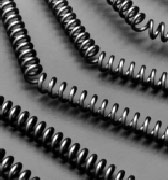 |
8) Why choosing APM elements is a better choice
|
a. APM elements is a better choice when firing to high temperature (Cone 5-6). Regular heating elements for Cone 04-06 will last very long (200 + firings).
b. For Cone 5-6, the APM elements cost long term is the same as replacing regular elements 3-4 times during that same period. APM elements cost 4 times more but they last 4 time longer.
c. You are less likely to have a failure with ware in the kiln and therefore less opportunity for glaze firing damage
d. Less headache and labor maintaining the kiln.
e. Each time elements are replaced, the kiln’s brick flake and the heating elements sockets wears off not holing the element in it’s socket properly. Less element replacement, better kiln’s bricks condition.
|
|
More about firing an Electric Kiln